views
CNC turning service has revolutionized the manufacturing world by offering precision, efficiency, and flexibility in producing complex parts. At the heart of this process lies the choice of material, which significantly influences the final product’s quality, durability, and cost-effectiveness. Understanding the different materials used in CNC turning service is essential for manufacturers, engineers, and businesses aiming to optimize their production outcomes.
This article explores the various materials commonly employed in CNC turning services, highlighting their properties, advantages, and typical applications. From metals to plastics, each material presents unique characteristics that determine its suitability for specific projects and industries.
Metals: The Backbone of CNC Turning Service
Metals are the most widely used materials in CNC turning service due to their strength, durability, and machinability. Among metals, aluminum, steel, and brass stand out as popular choices, each offering distinct benefits tailored to various industrial needs.
Aluminum is prized for its lightweight nature and excellent corrosion resistance. It is relatively easy to machine, making it ideal for rapid prototyping and production of aerospace, automotive, and consumer electronics parts. Steel, on the other hand, offers superior strength and hardness, suitable for components that require heavy-duty performance, such as in construction and machinery. Brass, known for its machinability and aesthetic appeal, is frequently used for decorative parts and fittings where both functionality and appearance matter.
Stainless Steel: For Durability and Corrosion Resistance
Stainless steel is a critical material in CNC turning service when corrosion resistance and strength are paramount. Its unique composition, including chromium, makes it resistant to rust and oxidation, which is essential in harsh environments like marine, chemical processing, and medical industries.
Despite its toughness, stainless steel is highly machinable using advanced CNC turning techniques, allowing for the creation of precision components such as surgical instruments, food processing equipment, and architectural fixtures. While it may require more cutting power than softer metals, modern CNC machines equipped with appropriate tooling handle stainless steel efficiently, ensuring high-quality finishes and dimensional accuracy.
Plastics: Lightweight and Versatile Alternatives
While metals dominate CNC turning service, plastics are gaining traction due to their versatility, lightweight properties, and resistance to chemicals and moisture. Common plastics used include nylon, acrylic, and polycarbonate, each serving specialized purposes across different sectors.
Nylon is favored for its toughness and wear resistance, making it suitable for gears, bushings, and insulators. Acrylic, known for its clarity and aesthetic quality, is often used for display cases and lighting fixtures. Polycarbonate offers high impact resistance and transparency, widely used in protective equipment and automotive components. CNC turning plastics allows for rapid manufacturing of complex shapes with less tooling wear and reduced production costs compared to metals.
Exotic Materials: Expanding the Horizons of CNC Turning
Beyond conventional metals and plastics, CNC turning service also accommodates exotic materials like titanium, Inconel, and carbon fiber composites, expanding the possibilities for high-performance applications.
Titanium is renowned for its exceptional strength-to-weight ratio and corrosion resistance, making it indispensable in aerospace, medical implants, and high-performance sports equipment. Inconel, a nickel-chromium superalloy, withstands extreme temperatures and corrosion, perfect for turbine blades, chemical reactors, and aerospace components. Carbon fiber composites, while not metals, are increasingly machined using CNC turning for their remarkable strength, stiffness, and lightness in automotive and aerospace industries, allowing for innovative design and performance enhancements.
Factors Influencing Material Selection in CNC Turning Service
Choosing the right material for CNC turning service depends on multiple factors including mechanical properties, environmental conditions, cost, and machining capabilities. Understanding these considerations helps manufacturers balance performance and budget effectively.
Mechanical properties such as tensile strength, hardness, and thermal conductivity dictate how a material responds under stress and heat during machining and in its intended use. Environmental factors like exposure to moisture, chemicals, and temperature extremes determine the need for corrosion resistance or thermal stability. Cost remains a crucial consideration, as exotic materials may offer superior qualities but at a premium price. Additionally, machinability influences production speed and tool wear, affecting overall efficiency and quality. Careful evaluation of these factors ensures the selection of an optimal material for each CNC turning project.
Conclusion
CNC turning service is a versatile manufacturing process that thrives on the diversity of materials it can work with. Metals like aluminum, steel, and stainless steel dominate due to their strength and durability, while plastics offer lightweight and cost-effective alternatives. Exotic materials further push the boundaries of innovation, enabling specialized applications in aerospace, medical, and high-performance industries.
Understanding the characteristics and advantages of different materials is crucial for selecting the best option tailored to specific requirements. By leveraging the right materials, CNC turning service can deliver precision parts that meet stringent performance criteria, driving advancements in manufacturing and product development.
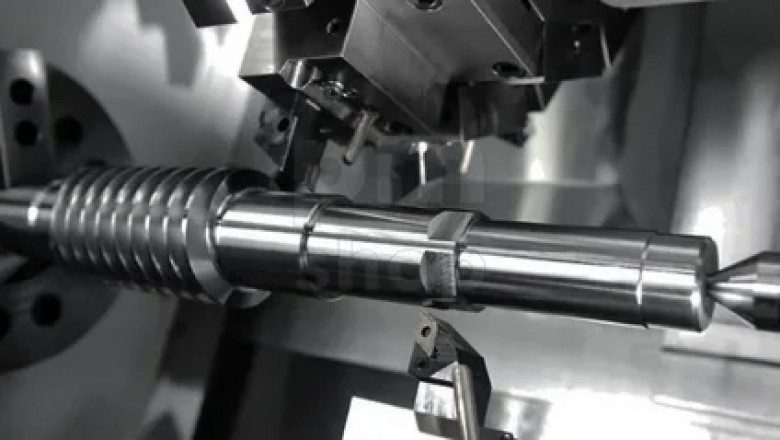
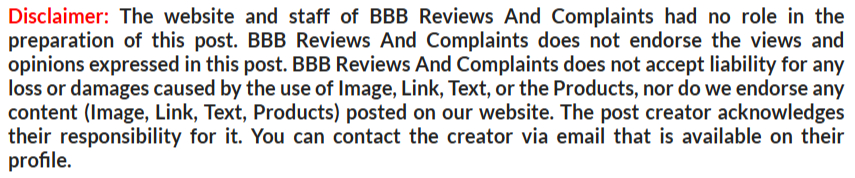
Comments
0 comment