views
Ignoring Reliability Centered Maintenance Could Be Costly
In today's fast-paced industrial world, equipment downtime is costly—both in terms of money and productivity. If your operations are plagued by unexpected equipment failures, you might be missing a critical strategy to avoid those disruptions. Reliability Centered Maintenance (RCM) is a proven method that helps businesses identify the most effective way to maintain equipment, ensuring reliability, reducing costs, and improving the overall efficiency of operations.
When you ignore RCM, you're not just risking your machinery; you're losing money every time a piece of equipment breaks down prematurely. The key to preventing these failures lies in understanding mean time between failure (MTBF), a valuable metric used to predict when a machine is likely to fail, allowing you to plan maintenance accordingly.
In this article, we’ll explore why RCM is a critical component of any maintenance strategy, how MTBF calculation plays a role in identifying weaknesses in your systems, and how RCM can save you money by reducing costly breakdowns and maximizing your equipment's lifespan.
The High Cost of Ignoring RCM
Many businesses fall into the trap of reactive maintenance, waiting until a machine fails to address its issues. This "run-to-fail" strategy may seem easier in the short term, but it comes with significant hidden costs, such as:
-
Unexpected Downtime – When equipment breaks down unexpectedly, your operations come to a halt. This downtime can result in lost productivity, missed deadlines, and frustrated customers.
-
Expensive Repairs – Reactive repairs tend to be more expensive than planned maintenance. When a piece of equipment fails suddenly, you're often forced to pay premium rates for emergency repairs.
-
Reduced Equipment Lifespan – Without proper maintenance, machines wear down more quickly, leading to premature failure and more frequent repairs.
-
Safety Risks – Equipment failures can also pose safety risks to your team, increasing the likelihood of accidents and potential legal consequences.
By incorporating RCM into your maintenance strategy, you can proactively address these risks, improving your equipment's reliability and reducing the overall cost of ownership.
What is Reliability Centered Maintenance (RCM)?
RCM is a systematic approach to maintenance that focuses on identifying and addressing the most critical components of your equipment. The goal is to ensure that each asset operates at its peak efficiency, minimizing downtime and the associated costs.
RCM involves evaluating each piece of equipment and determining the best approach to maintaining it based on factors such as:
-
The criticality of the equipment (how essential it is to your operations)
-
The failure consequences (what happens if the equipment fails)
-
The cost-effectiveness of maintenance strategies (balancing the cost of maintenance with the cost of failure)
By adopting RCM, you can create a more efficient and effective maintenance strategy that focuses on preventative and predictive maintenance rather than just reacting to failures as they happen.
The Role of MTBF in Predictive Maintenance
One of the most important concepts in RCM is Mean Time Between Failure (MTBF). MTBF is a metric that helps you predict how long a machine will operate before it’s likely to fail. Understanding MTBF allows you to plan maintenance, reducing the likelihood of unexpected failures.
Here’s how MTBF works:
-
MTBF is calculated by dividing the total operating time of a machine by the number of failures during that period.
-
For example, if a machine has operated for 10,000 hours and failed 10 times, its MTBF would be 1,000 hours.
By tracking MTBF, you can make data-driven decisions about when to service or replace equipment. This helps shift your strategy from reactive maintenance (waiting for a failure to occur) to predictive maintenance (acting before a failure happens).
Incorporating MTBF into your RCM strategy provides valuable insights into which equipment is most likely to fail and when, allowing you to plan your resources accordingly and avoid unexpected downtime.
How RCM Can Save You Money?
Implementing a Reliability Centered Maintenance program is one of the most effective ways to save money in the long term. Here’s how it works:
1. Reduced Equipment Downtime
With proactive maintenance strategies like RCM, you can predict and prevent equipment failures before they occur, minimizing unplanned downtime. This leads to higher productivity and fewer interruptions in your operations.
2. Lower Maintenance Costs
RCM helps you optimize your maintenance activities by focusing on the most critical components. Instead of performing routine maintenance on every piece of equipment, you can allocate resources more effectively, reducing unnecessary labor and parts costs.
3. Increased Equipment Lifespan
By keeping your equipment in optimal condition, you can extend its useful life. RCM ensures that your assets are well-maintained, which delays the need for costly replacements and ensures the longevity of your machinery.
4. Improved Resource Allocation
With RCM, you can prioritize maintenance tasks based on the criticality of each piece of equipment. This allows you to allocate your resources—whether that's labor, materials, or budget—more effectively, ensuring the highest return on investment.
Steps to Implement RCM
Adopting RCM doesn’t happen overnight, but with careful planning and execution, it can transform your maintenance approach. Here are the key steps to get started:
-
Assess Your Current Maintenance Strategy: Evaluate your existing maintenance practices and identify areas where RCM could make the most impact.
-
Identify Critical Assets: Determine which equipment is most essential to your operations and focus your RCM efforts on these assets.
-
Evaluate Failure Modes: Analyze your equipment’s failure modes and determine the consequences of each failure. This will help you decide which equipment requires more frequent or intensive maintenance.
-
Develop an RCM Program: Develop a maintenance program that incorporates predictive maintenance based on MTBF, failure modes, and criticality assessments.
-
Monitor and Adjust: Once your RCM program is in place, continuously monitor its effectiveness and make adjustments as needed to improve reliability.
Conclusion
Ignoring RCM could cost you more than you think. The expenses associated with unplanned downtime, emergency repairs, and reduced equipment lifespan add up quickly. By integrating RCM and understanding mean time between failure, you can predict and prevent failures, saving money and improving the overall efficiency of your operations.
Start implementing Reliability Centered Maintenance today to keep your equipment running smoothly and avoid costly breakdowns. Let MicroMain help you design a maintenance strategy that works for your business.
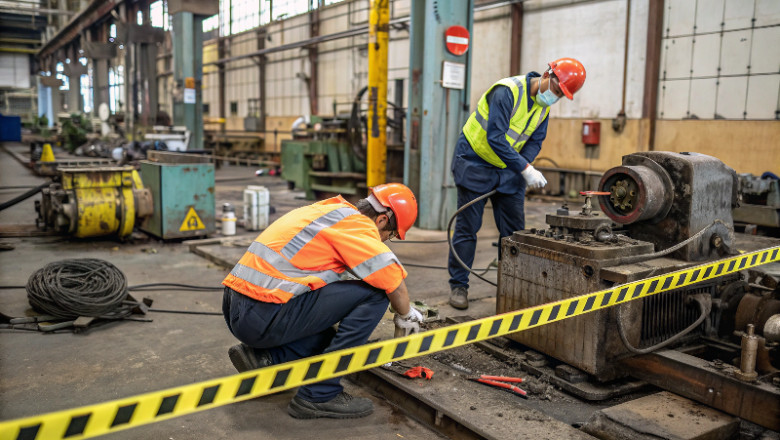
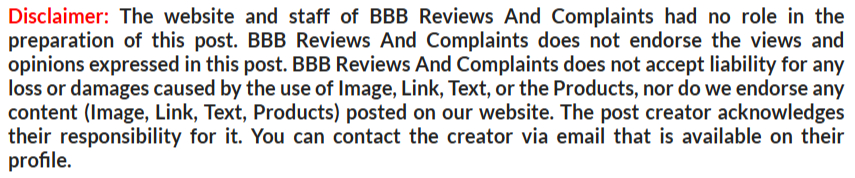
Comments
0 comment